DENAIS® HCWI, ASTM A532 Class III Type A, is a high chrome white iron which is a hypoeutectic structure consisting of very hard primary and secondary carbides in a matrix of martensite. By centrifugal molding process, a target thickness of HCWI alloy layer is lined on inner side of steel pipe. The straight pipe can be seamless or DSAW or customer-specified API standard steel pipe. The elbow is hot crucible elbow, also lined with HCWI alloy layer, which not only has the wear resistance, but also has high mechanical properties and pressure resistance.
Our engineered chemistry together with our proprietary heat treatment allows us to harden HCWI alloy to a minimum of 600 BHN. Dimensions are calculated to allow for dimensional changes during the hardening process.
This alloy has very good abrasion resistant properties, especially against gouging, grinding and scratching. It meets the requirements for many applications such as mining crusher liners, chute liners, ball mill liners (and lifter bars), slurry pumps, frac pumps, dredge pumps, impellers, oil sands applications, concrete rock crushing and recycling-machine parts (blow bars).
SUPPERIOR ABRASION RESISTANCE?
Chrome white iron is comprised of carbides and martensite. This combination makes chrome white iron exceptionally wear resistant and hard. The carbides, in form of ‘M7C3’ type, in chrome white iron have a hardness range of 1500-1800HV and are primarily eutectic carbides. These ‘Ka’ type carbides form as bundles of hollow hexagonal rods. The growth of these rods will drastically affect the properties of the casting, which is controlled through the careful engineering of the chemical composition.
Abrasion resistance is the property most desired when selecting a chrome white iron casting. At the foundry level the microstructure (carbides and martensite) is controlled to maximize the abrasion resistance for an application. There are many phenomena at work during cutting, gouging or scratching types of abrasion. The presence of carbides, the fatigue resistance and the toughness of high chrome white iron all play an important role in its abrasion resistance.
In a nutshell - the carbides in the matrix allow chrome white iron to have such exceptional wear life.

Cost of Wear and Corrosive
Because of its unique microstructure, high chrome white iron offers superior abrasion resistance, heat and corrosive resistance over other alloys, including steel and CCO. By replacing steel or CCO with high chrome white iron you can significantly extend the wear life of a casting or product. This reduces the total amount of material used over the life of a project, saving downtime and money.

Although the initial upfront costs of using DENAIS® HCWI might be slightly higher, the superior performance results in a lower total cost of ownership. Meaning DENAIS® HCWI products pay for themselves over and over again.

*PLEASE NOTE: Graphical representation is for illustrative purposes only. Actual performance and cost savings may differ depending on factors such as the type, size, velocity and density of particles within the media that the product is exposed to.
Typically, if the application involves transporting an abrasive media, using chrome white iron significantly extends the life of the part, reducing downtime in the process and resulting in substantial cost savings
Mining crusher liners
Oil sands applications
Chute liners
Ball mill liners (and lifter bars)
Slurry pumps
Frac. pumps
Dredge pumps
Pumps impellers and suction or bearing liners
Concrete rock crushing and recycling-machine parts(blow bars, anvils and throw shoes).
In severe applications (like flue gas desulfurization) consider using a 28% - 30% Cr alloy. Please contact DENAIS
Typical Hardness |
Brinell (depends on thickness) |
As-Cast | 450-550 |
Annealed | 300-450 |
Hardened | 600-700 |
WearLoss: 0.0004g/12hrs | |
Coefficient of Thermal Expansion: 1.2X107Ɛ/C | |
Density: 8.0g/cm3 |

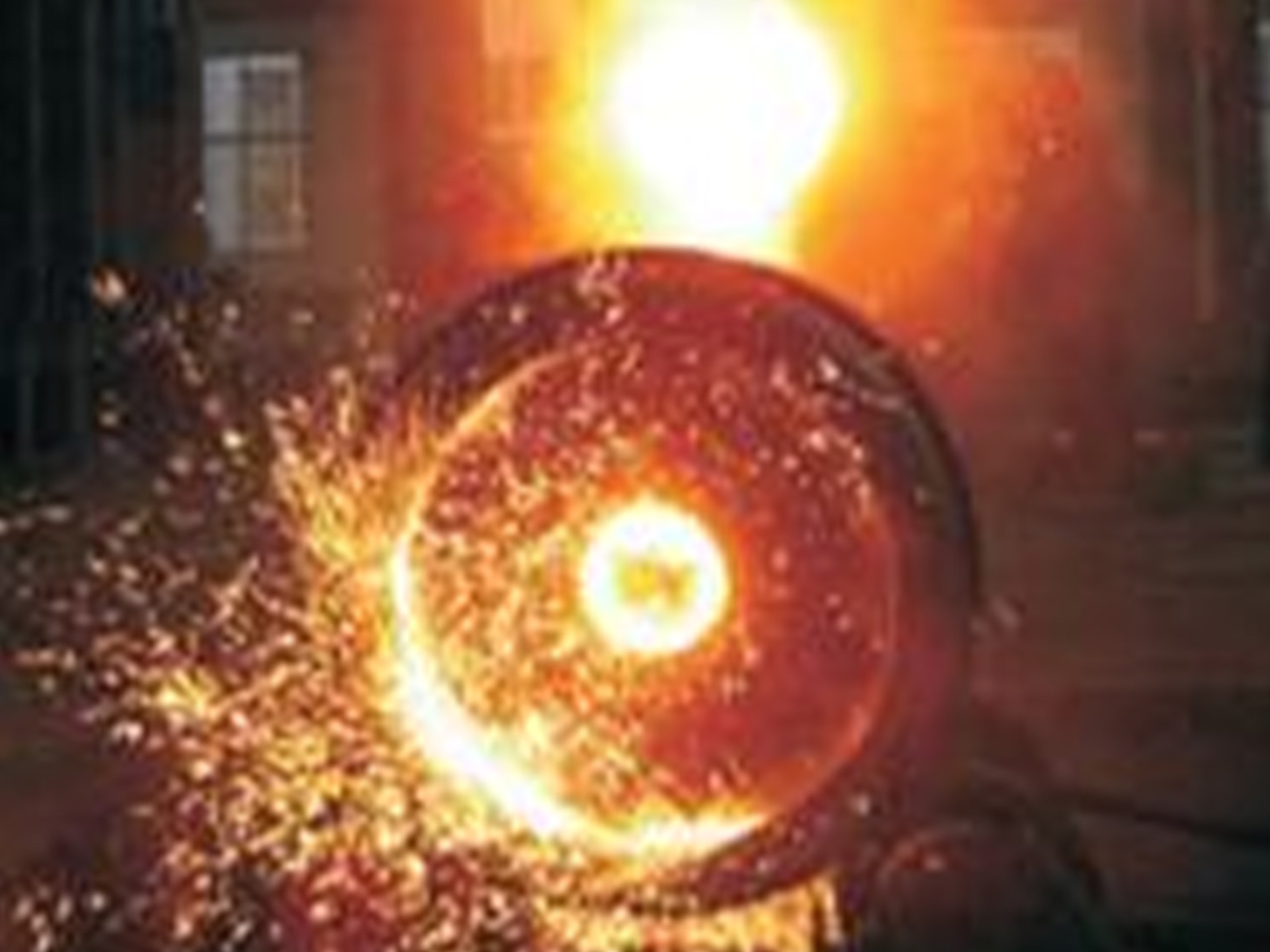


DENAIS® HCWI Lined Steel Pipe
Typical Connection: Flange Connection
Nominal Dia.DN |
Steel Pipe Spec. |
Inner Lining Thickness (mm) |
Unit Length (m) |
100 | Φ108x4 | Up to 65 | Up to 6 |
125 | Φ133x4 | ||
150 | Φ159x5 | ||
175 | Φ194x6 | ||
200 | Φ219x6 | ||
225 | Φ245x6 | ||
250 | Φ273x6 | ||
300 | Φ325x7 | ||
350 | Φ377x7 | ||
400 | Φ426x7 | ||
450 | Φ480x7 | ||
500 | Φ530x8 | ||
600 | Φ630x8 | ||
700 | Φ720x10 | ||
800 | Φ820x10 | ||
900 | Φ920x10 | ||
1000 | Φ1020x10 | ||
1200 | Φ1220x10 |
*We offer customer design service for non-standard products.
DENAIS® HCWI Lined Elbow
Typical Connection: Flange Connection

Nominal Dia.DN |
Steel Pipe Spec. |
Inner Lining Thickness (mm) |
Bending Radius (mm) |
100 | Φ108x4 | Up to 50 | 150 |
125 | Φ133x4 | 190 | |
150 | Φ159x5 | 230 | |
175 | Φ194x6 | 260 | |
200 | Φ219x6 | 300 | |
225 | Φ245x6 | 340 | |
250 | Φ273x6 | 375 | |
300 | Φ325x7 | 450 | |
350 | Φ377x7 | 525 | |
400 | Φ426x7 | 600 | |
450 | Φ480x7 | 675 | |
500 | Φ530x8 | 750 | |
600 | Φ630x8 | 900 | |
700 | Φ720x10 | 1050 | |
800 | Φ820x10 | 1200 | |
900 | Φ920x10 | 1350 | |
1000 | Φ1020x10 | 1500 | |
1200 | Φ1220x10 | 1800 |
*We offer customer design service for non-standard products.
DENAIS® HCWI Lined Tee Pipe
Typical Connection: Flange Connection

Nominal Dia.DN |
Steel Pipe Spec. |
Inner Lining Thickness (mm) |
Main Pipe Length (mm) |
Branch Height H (mm) |
|
L1 | L2 | ||||
100 | Φ108x4 | UP to 65 | 150 | 150 | 150 |
125 | Φ133x4 | 190 | 190 | 190 | |
150 | Φ159x5 | 205 | 205 | 205 | |
175 | Φ194x6 | 230 | 230 | 230 | |
200 | Φ219x6 | 230 | 230 | 230 | |
225 | Φ245x6 | 240 | 240 | 240 | |
250 | Φ273x6 | 280 | 280 | 280 | |
300 | Φ325x7 | 305 | 305 | 305 | |
350 | Φ377x7 | 350 | 350 | 350 | |
400 | Φ426x7 | 400 | 400 | 400 | |
450 | Φ480x7 | 450 | 450 | 400 | |
500 | Φ530x8 | 500 | 500 | 450 | |
600 | Φ630x8 | 600 | 600 | 500 | |
700 | Φ720x10 | 700 | 700 | 550 | |
800 | Φ820x10 | 800 | 800 | 650 | |
900 | Φ920x10 | 900 | 900 | 700 | |
1000 | Φ1020x10 | 1000 | 1000 | 800 | |
1200 | Φ1220x10 | 1100 | 1100 | 850 |
*We offer customer design service for non-standard products.
DENAIS® HCWI Lined Steel Pipe Spools