DENAIS® SOSR: A high performance rubber compound designed to provide resistance to oils, wet abrasion and elevated temperatures, which is specially designed to meet the rigorous demands of the oil sands industry.
It exhibits outstanding strength, resilience, and resistance to cutting and tearing, giving superior performance in wet abrasion conditions. Our sustained performance advantage in the rubber industry lies in our well-proven manufacturing process, which creates a product that provides superior performance when compared to other wear materials. DENAIS® SOSR is extremely strong, tough and resilient. When this is combined with the excellent tear, cut and abrasion resistance, our rubber products are irreplaceable in abrasion trouble spots. By using the highest quality raw material, combined with our professional manufacturing process, we deliver reduced operational down time and lower total ownership costs
The DENAIS® SOSR is extremely versatile and suitable as protective lining for a variety of surfaces to minimize wear and corrosion of the base structure. Even it is specially designed for the rigorous oil sand application, the excellent properties of SOSR make it suitable for many other applications. Typical lining applications include:
Chute lining
Pipe lining
Vessel lining
Hose construction
In addition to its versatility, DENAIS® SOSR products are lighter and more flexible than other wear liner materials such as steel and ceramics. This aids with installation and maintenance. Both our cured and uncured rubber products can be manufactured with varying thicknesses.
Outstanding abrasion resistance
Oil resistant
Chemical resistant
Weather resistant
Ageing resistant
Excellent rebound resilience
To select the most appropriate compound for an application, many factors need to be taken into account. Understanding the following factors is critical to making the right selection:
In order to achieve the best possible operating economy and the longest service life, it is usual to increase rubber thickness within certain limits to cope with larger and heavier particles.
Impact of particles from increasing height also requires increased rubber thickness to absorb compressive forces.
As the particle hits the surface, the rubber deforms, absorbing the kinetic energy of the particle. The resilient nature of rubber returns most of this energy to the particle, causing it to rebound. There will be little or no wear and no permanent deformation.
However, if the particle momentum is too great relative to the rubber thickness, the impact force cannot be absorbed and the rubber may cut or tear.
The diagram demonstrates the reason rubber outperforms steel in many abrasive environments. It is the ability of the rubber to absorb an impact and then return the energy from the impact back to the particle that results in higher wear performance.
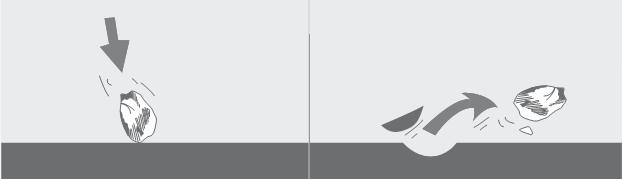
Abrasive particle striking non-elastic metal surface. Conversion of kinetic energy into impact, friction and noise.

Abrasive particle striking resilient rubber surface. Rubber deforms under load and returns most of kinetic energy to the particle without rate of wear experienced above.
In impact and sliding abrasion situations there is a critical speed above which elastomers are unable to recover and absorb energy. In this case, the product’s resilience cannot be used to its full extent and the surface may deteriorate more rapidly.
The angle of impact of the particle relative to the wear surface is of great importance in designing chutes, hoppers and rubber linings in general. The effect of different angles on wear rate can be significant.
At 90° impact angle, resilience is the major factor in resisting wear, but as the impact angle reduces to around 50°, tear resistance becomes more important. At very low impact angles, slurries are best handled by flat surface. This applies to pulley lagging and applications involving general sliding wear, where the abrasive force is tangential or in-plane to the surface.

Selection Criteria for Impact Angle and Sliding Wear
In broad terms, harder rubbers are preferred for combating high impact/cutting forces that often occur when handling coarse materials. DENAIS® SOSR rubber gives excellent results when used in abrasive slurry service or sliding abrasion where fine to medium particles are being handled.
Other physical properties can often play a significant role in optimising performance. For example, good resilience is required when screening sticky materials. Rubber elongation is the important factor in the design of fabricated seals and bellows. The key to specifying the correct rubber is in selecting the best combination of properties to suit the application.
The temperature of the application in which the rubber will be used is important. The temperature limits of DENAIS® SOSR can be used in applications where temperatures reach 100°C/212°F.
It is also important to take into account the temperature limits of the adhesive system being used if rubber lining is taking place. Most rubber adhesive systems are limited to temperatures up to 90°C/194°F.
Different rubber compounds exhibit varying degrees of resistance to chemicals. Natural rubber, for example, is unsuitable for use in contact with hydrocarbons. In this situation, DENAIS® SOSR is more suited.
We offer a range of rubber materials that maximise potential applications in chemical environments.
The chemical composition of the slurry or application should always be verified to confirm that the rubber being selected is suitable.
Occupational health and safety regulations in many countries require that industry complies with specific noise level standards for the protection of employees.
Rubber lined structures and fabrications play a prominent role in creating a more comfortable working environment. This is done by reducing noise and vibrations, often with the additional benefit of controlling dust dispersion.
DENAIS ® SOSR Lined Rubber Hose & Reducer
Typical Pressure: Up to 650psi/48bar design pressure
Typical Connection: Flange Connection

Nominal Dia. DN |
Steel Pipe Spec. |
Inner Lining Thickness (mm) |
Unit Length (m) |
100 | Φ108x4 | Up to100 | Up to11.8 |
125 | Φ133x4 | ||
150 | Φ159x5 | ||
175 | Φ194x6 | ||
200 | Φ219x6 | ||
225 | Φ245x6 | ||
250 | Φ273x6 | ||
300 | Φ325x7 | ||
350 | Φ377x7 | ||
400 | Φ426x7 | ||
450 | Φ480x7 | ||
500 | Φ530x8 | ||
600 | Φ630x8 | ||
700 | Φ720x10 | ||
800 | Φ820x10 | ||
900 | Φ920x10 | ||
1000 | Φ1020x10 | ||
1200 | Φ1220x10 |
*We offer customer design service for non-standard products.
DENAIS® SOSR Lined Rubber Elbow
Typical Pressure: Up to 650psi/48bar design pressure
Typical Connection: Flange Connection

Nominal Dia. DN |
Steel Pipe Spec. |
Inner Lining Thickness (mm) |
Bending Radius (mm) |
100 | Φ108x4 | Up to100 | 150 |
125 | Φ133x4 | 190 | |
150 | Φ159x5 | 230 | |
175 | Φ194x6 | 260 | |
200 | Φ219x6 | 300 | |
225 | Φ245x6 | 340 | |
250 | Φ273x6 | 375 | |
300 | Φ325x7 | 450 | |
350 | Φ377x7 | 525 | |
400 | Φ426x7 | 600 | |
450 | Φ480x7 | 675 | |
500 | Φ530x8 | 750 | |
600 | Φ630x8 | 900 | |
700 | Φ720x10 | 1050 | |
800 | Φ820x10 | 1200 | |
900 | Φ920x10 | 1350 | |
1000 | Φ1020x10 | 1500 | |
1200 | Φ1220x10 | 1800 |
*We offer customer design service for non-standard
DENAIS® SOSR Lined Rubber Tee Hose
Typical Pressure: Up to 650psi/48bar design Pressure
Typical Connection: Flange Connection

Nominal Dia. DN |
Steel Pipe Spec. |
Inner Lining Thickness (mm) |
Main Pipe Length (mm) |
Branch Height H (mm) | |
L1 | L2 | ||||
100 | Φ108x4 | UP to 100 | 150 | 150 | 150 |
125 | Φ133x4 | 190 | 190 | 190 | |
150 | Φ159x5 | 205 | 205 | 205 | |
175 | Φ194x6 | 230 | 230 | 230 | |
200 | Φ219x6 | 230 | 230 | 230 | |
225 | Φ245x6 | 240 | 240 | 240 | |
250 | Φ273x6 | 280 | 280 | 280 | |
300 | Φ325x7 | 305 | 305 | 305 | |
350 | Φ377x7 | 350 | 350 | 350 | |
400 | Φ426x7 | 400 | 400 | 400 | |
450 | Φ480x7 | 450 | 450 | 400 | |
500 | Φ530x8 | 500 | 500 | 450 | |
600 | Φ630x8 | 600 | 600 | 500 | |
700 | Φ720x10 | 700 | 700 | 550 | |
800 | Φ820x10 | 800 | 800 | 650 | |
900 | Φ920x10 | 900 | 900 | 700 | |
1000 | Φ1020x10 | 1000 | 1000 | 800 | |
1200 | Φ1220x10 | 1100 | 1100 | 850 |
*We offer customer design service for non-standard products.



PROPERTY | UNIT | TEST STANDARD | DENAIS®SOSR |
Polymer Type | Polychloroprene | ||
Hardness (A) | Shore A | ISO48 | 54 |
Tensile Strength | Mpa | ISO37 | 19.8 |
Elongation at Break | % | ISO37 | 606 |
Tear Strength | N/mm | ISO34 | 31 |
Low Temperature Brittleness | ℃ | GB/T1682 | -51℃ |
Rebound Resilience | % | ISO4662 | 58 |
Oil Resistance(Volume Swell) | % | ISO1817 | 19.8 |
Abrasion Resistance | % | ISO4649 | 26 |
Accelerated Ageing and Heat Resistance |
100℃ for 72 Hours | ISO188 | △Hardness:6 △Tensile Strength:10.6% △Elongation at Break:-13.4% |
Specific Gravity | g/cm³ | ISO2781 | 1.32 |
Operating Temperatures (continuous use) |
℃ | -40℃ to +100℃ |
DENAIS® SOSR Lined Rubber Hose, Reducer & Elbow